Understand the Working Principle of the Hydraulic Breaker
Operators achieve optimal performance when they clearly understand how the гидравлический молот works. This equipment uses hydraulic oil pressure to power a piston that strikes a tool, breaking rocks or concrete. When users grasp this simple mechanism, they avoid common errors such as dry firing or misalignment.
Maintaining consistent oil flow and pressure ensures the tool hits effectively. Гидравлический молот users often overlook the importance of hydraulic compatibility. Ensure the carrier machine provides the correct oil flow rate and pressure range, which maximizes impact force and tool longevity.
Frequent misfires or performance drops usually signal mismatched specifications. Users must check the breaker’s requirements and compare them with the carrier output before each job. This step protects both machines and improves efficiency.
Choose the Right Tool for the Material
Operators boost productivity when they match the correct chisel type with the target material. Гидравлический молот attachments come in different shapes for a reason. For example:
- Moil points suit general demolition
- Chisel tools perform best on concrete
- Blunt tools apply maximum force on large rocks
Failing to select the right tool increases wear and reduces breaking power. By choosing the suitable accessory, users reduce cycle times and save fuel. In every case, material hardness determines the ideal tool shape.
Operators should inspect tool wear regularly. A rounded or mushroomed tip lowers effectiveness and increases stress on the гидравлический молот. Replacing or sharpening the tool early prevents downtime and ensures clean breaks.
Maintain Proper Breaker Positioning During Operation
Correct positioning greatly affects productivity and component lifespan. Always place the гидравлический молот perpendicular to the surface. Angled strikes cause tool slippage, inefficient energy transfer, and damage to both the attachment and the base machine.
Operators must avoid using the breaker as a prying tool. This practice bends the tool shank, cracks internal seals, and leads to early failure. Instead, allow the breaker to perform short, controlled bursts. Move the tool slightly between hits to prevent excessive wear in one area.
Holding the breaker in a fixed spot for too long causes heat buildup and tool damage. Instead, operators should break material gradually and shift positions after every few seconds of impact. This technique spreads the stress evenly across the tool and target surface.
Follow a Strict Maintenance Schedule
Timely maintenance extends the service life of the гидравлический молот and ensures safe operation. Operators must perform daily inspections before starting work. They should look for the following:
- Leaks around hoses and connections
- Cracks on the housing or tool
- Abnormal sounds during operation
- Loose bolts and damaged bushings
Regular lubrication of the tool bushing prevents metal-to-metal wear. Operators must use the correct type and amount of grease at recommended intervals. Over-greasing causes a pressure buildup, while under-greasing leads to rapid wear.
Changing the hydraulic oil and filters on schedule prevents contamination and internal damage. Dirty oil reduces efficiency and leads to premature seal failure. Operators should also monitor nitrogen gas pressure inside the accumulator. Low gas levels reduce impact force and slow down work.
Train Operators Thoroughly Before Deployment
Skilled operation improves efficiency and minimizes machine wear. Companies should invest in training programs that teach safe handling, proper techniques, and routine maintenance. When operators understand their equipment, they reduce downtime and avoid costly repairs.
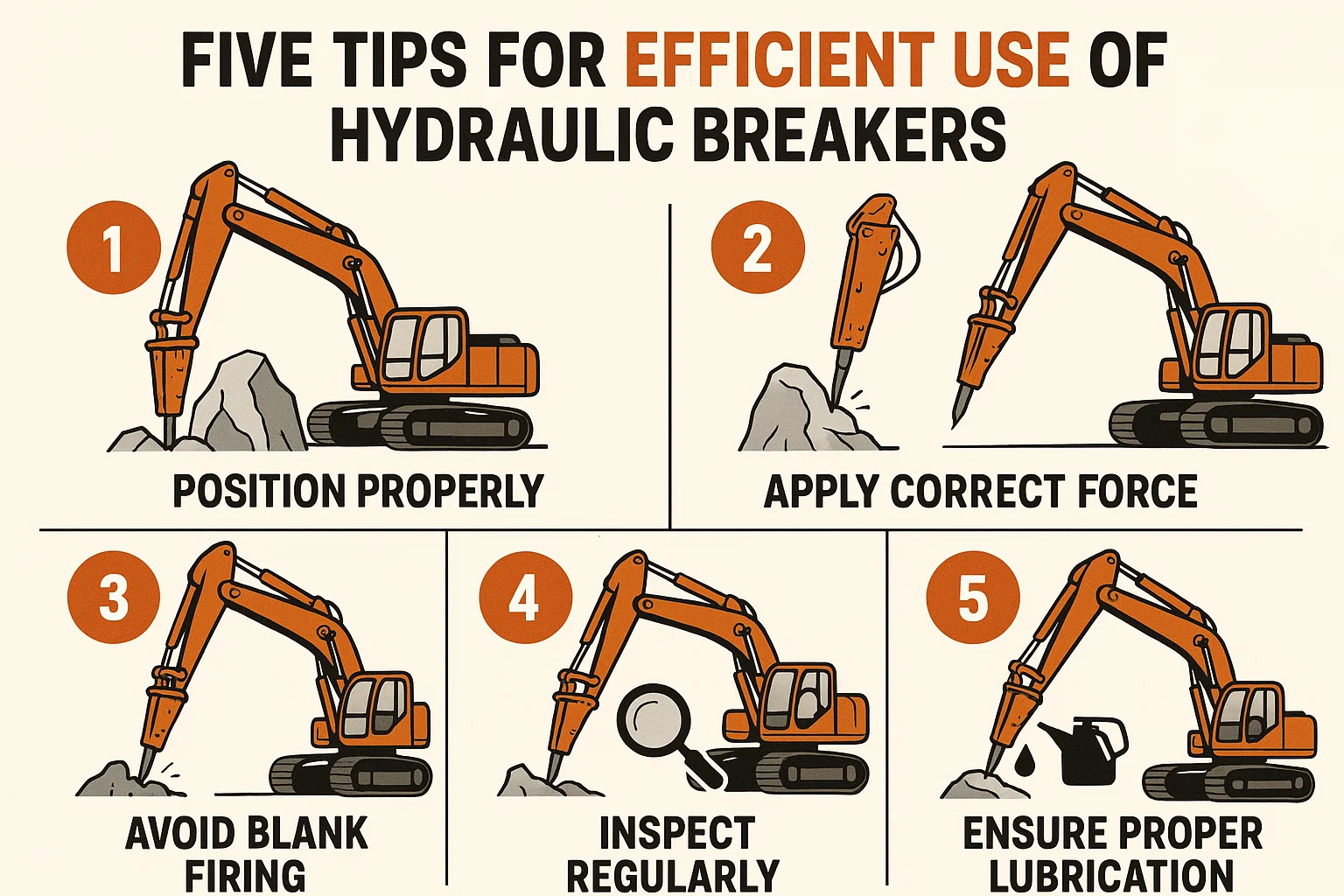
New users must learn how to match breaker size with the carrier’s hydraulic system. They should practice tool positioning and recognize signs of tool wear or internal damage. Ongoing training reinforces these practices and keeps performance consistent.
Training also prevents misuse, such as working in extreme temperatures without proper precautions. For example, in cold environments, operators must warm up hydraulic systems before heavy use. In hot weather, they must watch oil temperature to prevent overheating.
Common Questions About Hydraulic Breaker Operation
1. How do I prevent dry firing in my hydraulic breaker?
Dry firing happens when the tool runs without proper resistance from the surface. Operators can avoid this by ensuring the chisel always contacts the material before triggering impact. Using auto-stop features or shut-off valves also prevents damage from dry firing.
2. What oil flow range should I use for my breaker?
Каждый гидравлический молот has a recommended oil flow range, typically found in the technical manual. Using lower flow reduces impact power. Exceeding the maximum damages seals and the piston. Match the carrier’s output to the breaker’s requirement before operation.
3. How often should I replace the tool bit?
Replace the tool bit when the tip becomes rounded, mushroomed, or cracked. Daily inspection helps detect early signs of wear. Regular replacement maintains consistent force and protects internal components from unnecessary strain.
4. What causes frequent seal failures?
Contaminated oil, overheating, or incorrect gas pressure often cause seal failures. Operators must follow a strict maintenance schedule and monitor operating temperatures. Keeping hydraulic oil clean and maintaining proper nitrogen pressure prevents premature seal wear.
Recap of Key Points
Operators ensure top performance by mastering equipment knowledge, selecting the correct tool, maintaining proper technique, sticking to a strict maintenance routine, and undergoing continuous training. Each practice directly improves productivity, lowers operating costs, and extends machine life. Proper care of the гидравлический молот ensures consistent performance in every job environment.
Take Action with Beilite Hydraulic Breakers
Contact our support team for expert advice, product selection, or customized training. We provide reliable гидравлический молот solutions designed for efficiency and durability. Reach out now and optimize your worksite performance with Beilite.