The Impact of High-Temperature Environments on Hydraulic Breakers
High-temperature environments directly affect the operational performance and service life of hydraulic breakers. Under high-temperature conditions, the internal oil temperature of the equipment rises rapidly, the hydraulic system is subjected to greater pressure, seals are prone to aging, and metal components experience accelerated expansion. These issues reduce breaking efficiency, increase the risk of malfunctions, and result in unnecessary maintenance costs.
Operators must be aware of the destructive power of high temperatures and take timely measures to address them. Scientific maintenance of hydraulic breakers is key to ensuring construction efficiency and equipment safety.
Check the hydraulic oil temperature and maintain it within a reasonable range.
Excessively high hydraulic oil temperatures can cause a decrease in viscosity, reduced lubrication performance, and accelerated system wear. Most equipment recommends maintaining hydraulic oil temperatures between 50°C and 80°C. In regions where ambient temperatures exceed 35°C, the oil tank temperature should be checked using an infrared thermometer after the equipment has been running for 20 minutes.
If the oil temperature remains above 90°C for an extended period, the operator must immediately shut down the equipment. At this point, issues can be addressed by replacing the hydraulic oil with high-temperature, oxidation-resistant hydraulic oil or installing an oil cooler. Oil temperature control is a fundamental aspect of hydraulic breaker maintenance and directly impacts the equipment’s ability to operate stably over the long term.
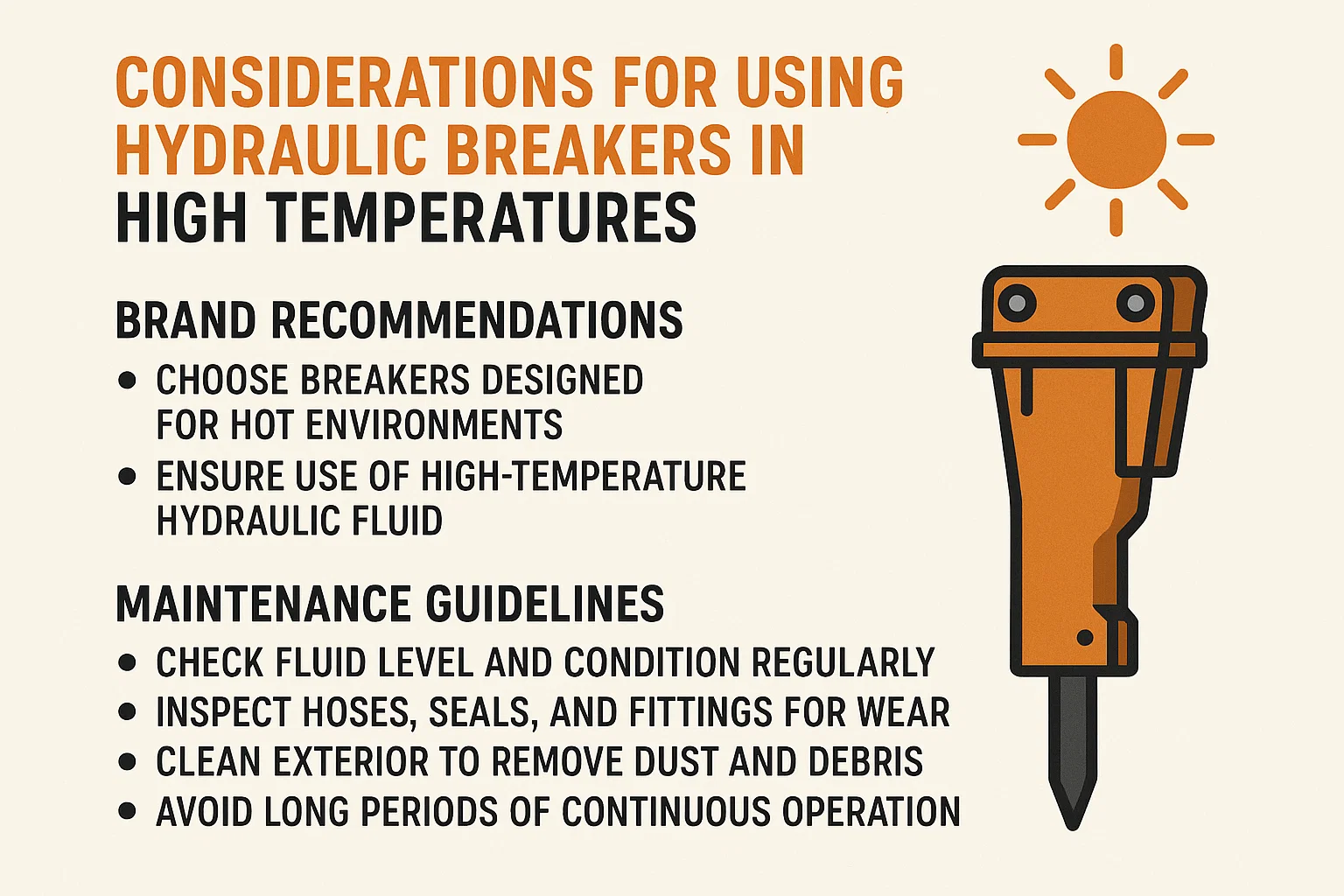
Regularly inspect hydraulic lines and fittings
In high-temperature environments, hydraulic lines are subjected to high pressure and thermal expansion, making them prone to oil leaks and ruptures. Operators should inspect hose connections daily for oil stains, cracks, or signs of loosening. High temperatures can also cause some aged rubber fittings to fail more quickly, so they must be replaced in advance.
Construction companies may opt for high-temperature-resistant braided hydraulic hoses to extend service life. Pipe routing should avoid close proximity to high-temperature components to minimize heat conduction risks.
Lubricant Selection and Refill Frequency Adjustment
High temperatures accelerate the decomposition of lubricants, and poor lubrication directly leads to increased wear on the piston rod and bushing. Operators should refill with high-temperature lubricant once a day based on the intensity of the work and the ambient temperature.
The use of calcium-based or composite lithium-based lubricants helps improve high-temperature resistance. Especially during continuous crushing operations, refilling with lubricant once an hour will significantly extend the service life of the breaker.
Timely removal of dust and debris from the surface of the breaker
Construction sites are often accompanied by large amounts of rocks and dust, which are more likely to adhere to equipment surfaces under high-temperature conditions. If not cleaned promptly, these particles may block cooling vents, impairing heat dissipation and potentially triggering high-temperature alarms.
After each day’s work, operators should use compressed air or a water gun to clean the hammer body, focusing on removing dust from the piston, bushings, and cooling components. Maintaining equipment cleanliness can effectively extend its service life.
Avoid prolonged continuous operation of equipment.
Continuous operation for more than two hours in high-temperature environments can cause thermal load accumulation in the internal components of the hydraulic breaker, increasing the likelihood of damage. It is recommended to adopt a cycle of “40 minutes of operation followed by 20 minutes of rest.”
During periods of intense sunlight (11 a.m. to 3 p.m.), minimize high-load operations. Scientific scheduling of construction time can help reduce equipment failure rates and ensure project progress.
Selecting a hydraulic breaker brand suitable for high-temperature environments
In high-temperature construction scenarios, selecting a brand with high-temperature resistance capabilities is particularly critical. Beilite hydraulic breakers feature a double-layer sealing structure to effectively prevent high-temperature oil leakage; the main components are cast using heat-resistant materials to ensure long-term stable operation without deformation.
Based on feedback from tropical and Middle Eastern construction environments, Beilite has launched multiple models of hydraulic breakers designed for high-temperature and high-load conditions, catering to diverse construction needs such as mining, tunneling, and road construction. Its products are widely used in high-temperature regions such as Africa, the Middle East, and Southeast Asia, and have earned a strong reputation.
Set equipment parameters reasonably to avoid abnormal loads.
High temperatures can easily cause abnormal fluctuations in the hydraulic system. Before starting the equipment, the operator must check whether the system pressure is within the standard range. Excessively high or low pressure may cause malfunctions.
During construction, avoid oblique strikes, empty strikes, or excessive downward pressure to reduce impact on the piston and drill rod. Before starting the equipment, idle for 5 minutes to allow the system to warm up slowly, which helps it enter a stable working state.
Use specialized sunshade tools and heat dissipation devices
To reduce the thermal load on equipment, physical heat dissipation tools such as sunshades, sunshade cloths, and fans can be installed on hydraulic breakers. If an external oil cooler is installed, the heat dissipation fins must be cleaned regularly to prevent dust blockage.
Some construction companies use hydraulic breakers with temperature-controlled fans, enhancing continuous operation capabilities in high-temperature environments. Installing cooling devices is a low-cost, high-return optimization measure and is recommended for consideration.
Operator Training and Implementation of Operating Procedures
Construction in high-temperature environments carries high risks, so operators must undergo professional training to understand the equipment’s heat dissipation structure, lubrication system, and abnormal warning mechanisms. Familiarity with equipment operating procedures helps operators respond quickly to sudden problems caused by high temperatures.
Before starting work, equipment operators must complete a checklist that includes oil temperature, lubrication, hose condition, and cooler operation. Strict adherence to operating procedures is a prerequisite for ensuring safe equipment operation.
After-sales service and spare parts support ensure stable operation
Choosing a brand with fast after-sales service response and ample spare parts supply can significantly reduce the risk of downtime during high-temperature operations. Beilite offers 7×24-hour after-sales service and guarantees the supply of original factory parts, with multiple service centers both domestically and internationally.
Using original seals, lubricants, and drill rods can enhance the machine’s ability to withstand high temperatures. In the event of equipment failure, technical support and replacement solutions can be obtained immediately, minimizing project losses.
In high-temperature environments, hydraulic breakers face multiple challenges such as hydraulic oil overheating, insufficient lubrication, and component aging. Operators need to address these issues by managing oil temperature, inspecting pipelines, maintaining lubrication, and adhering to operating procedures to comprehensively enhance the equipment’s ability to withstand high temperatures.
Selecting brands with strong high-temperature adaptability and comprehensive after-sales service, such as Beilite breakers, can effectively reduce failure rates, improve operational efficiency, and ensure construction progress.
Contact Beilite immediately to obtain high-temperature operation breaker solutions
If you are working in high-temperature regions or your equipment frequently shuts down due to thermal protection, please contact Beilite immediately to obtain a customized solution. We provide product selection recommendations, operational guidance training, and rapid spare parts services to help you easily tackle high-temperature construction challenges.
Frequently Asked Questions
- How often should hydraulic oil be replaced in high-temperature environments?
In high-temperature conditions, hydraulic oil ages more quickly. It is recommended to replace it every 500 hours. If the equipment is operating continuously under high intensity, replacement should be done every 300 hours. - Can hydraulic breakers operate continuously around the clock?
Continuous operation without breaks is not recommended. After 40–60 minutes of continuous operation, the machine should be shut down for 10–20 minutes to allow for cooling, which helps extend the equipment’s lifespan. - What type of grease is most suitable for high-temperature environments?
We recommend using lithium-based grease, which has superior high-temperature resistance. Beilite offers specialized grease designed for use in environments above 40°C. - How can one determine if the breaker has failed due to high temperatures?
Common symptoms include oil temperature alarms, weak striking force, abnormal noise, and rapid loss of lubricant. Infrared temperature measurement and pressure testing can be used to confirm whether the abnormality is caused by high temperatures.