1. Definition and Function of Hydraulic Breakers
Hydraulic breakers, which play a crucial role in hydraulic excavators, are also commonly installed on excavator loaders or wheel loaders for breaking operations. In Japan and South Korea, these tools are typically referred to as hydraulic breakers or hydraulic rock breakers, while companies in Finland and Germany more frequently use the term hydraulic hammers. In China, manufacturers and users may refer to it by different names, but regardless of the terminology, they all refer to the same piece of equipment. A hydraulic breaker is an essential tool that utilizes liquid static pressure to drive piston movement, thereby achieving high-speed impact on the chisel to perform breaking operations. This tool uses liquid static pressure as its power source, driving the reciprocating motion of the piston. During the piston stroke, it rapidly strikes the chisel rod, utilizing the chisel rod to crush solid materials such as ore and concrete. This article will uniformly refer to it as a hydraulic hammer.
2. Hydraulic Hammer Models and Numerical Meanings
Hydraulic hammer models are typically composed of letters and numbers, and different manufacturers may assign different meanings to the specific numbers in these models. Therefore, when interpreting hydraulic hammer models, it is necessary to understand them in conjunction with each manufacturer’s naming conventions. Models are typically composed of letters and numbers, with the numbers potentially representing applicable machine weight, bucket capacity, self-weight, drill rod diameter, and impact energy, among other complex and diverse meanings. The numbers in hydraulic hammer model numbers are often used to indicate the machine weight range of the excavators they are suitable for. Similarly, these numbers may also represent the bucket capacity of the excavators the hydraulic hammers are suitable for. Additionally, the numbers in the model number may directly reflect the self-weight of the hydraulic hammer. Furthermore, the numbers in the model number are often used to indicate the chisel diameter of the hydraulic hammer and the impact energy it possesses. However, in some cases, the numbers in the model number are solely used to distinguish between different design serial numbers of hydraulic hammers.
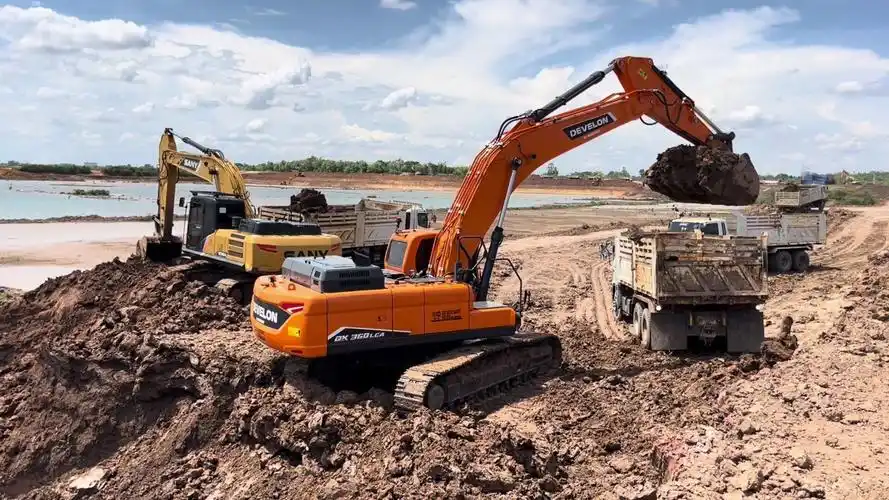
3. Selection of Hydraulic Hammers
After understanding the rich meanings represented by the numbers in hydraulic hammer model numbers, excavator users can make more informed decisions when selecting and matching hydraulic hammers. Selection should be based on the model number, bucket capacity, machine weight, and manufacturer’s guidelines, while also considering the accuracy and influencing factors of impact energy standards. Users can directly select the appropriate hydraulic hammer model based on the actual weight of the excavator. When selecting a hydraulic hammer based on the excavator’s bucket capacity, the weight of the excavator’s bucket and the density of the sand and soil must be considered. If the numbers in the hydraulic hammer model represent its mass, chisel diameter, or impact energy, the selection process typically requires reference to the manufacturer’s selection guide table or industry experience. It is worth noting that the Construction Industry Manufacturers Association (CIMA) in the United States has established a unified standard for hydraulic hammer impact energy (IE) testing methods for manufacturers of machine-mounted breakers.
4. Matching hydraulic hammers with excavators
When matching hydraulic hammers with excavators, users need to consider multiple factors comprehensively. First, weight matching is essential, as a hydraulic hammer that is too heavy or too light may affect the overall performance of the excavator. Factors such as oil volume, lifting capacity, and discharge pressure must be considered to ensure coordinated operation between the hydraulic hammer and the excavator. Second, power matching is critical, as it directly impacts the hydraulic hammer’s efficiency and the excavator’s power output. As an important component of the excavator, the hydraulic hammer’s weight must be supported by the excavator’s lifting capacity. The operation of the hydraulic hammer relies on the excavator’s hydraulic system, so matching must ensure the excavator can provide adequate hydraulic pressure. Typically, the flow rate required by the hydraulic hammer should be controlled between 60% and 80% of the excavator’s total flow rate to ensure optimal performance.
5. Hydraulic Hammer Seal Leakage and Prevention Measures
When oil leakage is detected in the breaker, the first step is to inspect the sealing areas for abnormalities. Oil leakage can result from various complex causes, requiring thorough inspection and repair, with attention to the interaction between seal condition and operating environment. If the primary seals show no abnormalities, further investigation into other potential causes is necessary. If leakage occurs under low-pressure conditions but not under high-pressure conditions, this is typically due to poor surface roughness of the assembly surfaces. To address this issue, improve the surface roughness and consider using seals with slightly lower hardness. Pay attention to the surface condition of various types of seals; for example, hardening or cracking of the main oil seal surface may be caused by abnormal high-speed operation or excessive working pressure. When addressing oil leakage issues, it is essential to carefully consider factors such as the working medium, pressure environment, and mechanical fit.